

- #Grbl controller cnc how to
- #Grbl controller cnc drivers
- #Grbl controller cnc software
- #Grbl controller cnc Pc
configure control gcode keyboard macros For Grbl, it will be "Grbl 1. 1e Type $ and press enter to have Grbl print a help message. Are you trying to move it with a G1? That requires a feedrate, i. Much like the max rate setting, each axis has its own acceleration value and are independent of each other. Say you set your feed rate to 1000 mm/min in your g code, clicking the 10- button decreases this by 10% so your machine is now feeding at 900 mm/min. Diagram Blok Perancangan Mesin CNC Router dengan Aplikasi GRBL 0. The GRBL Shield goes on top of the Arduino Uno. 9g but i have the same problem, when start picture go extremely slow. Actually Marlin on a Mega2560 and it'beds base64 method appears to operate out of running power at around feed prices of 7000. The ability to kill a move and flush the motion buffer is something we’d been asking for to provide better jogging performance. 5, G80 - Feed Rate Modes For Grbl, it will be "Grbl 1. Set this to the highest value $110-2 (Maximum feed rate) From the Grbl Configuration guide: $110, $111 and $112 – Max rate, mm/min. A green bar should appear at the bottom, which shows the progress of the upload. In GRBL, you set the max rates for the primary axes by modifying the $110, $111 and $112 options. Sometimes it doesn't work the first time. Set the baud rate to 115200 as 8-N-1 (8-bits, no parity, and 1-stop bit. This sets the maximum rate each axis can move. If I set a feed rate of 35 mm/min, that is processed correctly - but it needs two passes to cut the acrylic. Open the G code-all the axis should be“0”-then start to engrave, You can choose the “Feed hold” to pause the working when it has something, if something emergency happens, you can use the “Reset” or you can adjust the “Feed rate”. The feature will only increase or decrease your machine’s feed rate from the cut settings you selected before carving. If you use a high step/mm and you want to perform very fast movement Grbl should generate a lot of stepper pulse. 23: Invalid gcode ID:23: G-code command in block requires an integer value. 0 Rpm: Current Spindle speed in revolutions/min. (this is the limitation from grbl firmware it self) Z microsteps: 1 (no microsteps) 2 microsteps per step 4 microsteps per step 8 microsteps per step 16 microsteps per step 32 microsteps per step 5 microsteps per step 10 microsteps per step 20 microsteps per step 25 microsteps per step 40 microsteps per step. 9i Type $ and press enter to have Grbl print a help message. The maximum feed rate is around 400mm/min in X & Y direction and roughly 50mm/min along the Z axis. After doing some test pieces I discovered an issues with motions in a particular feed rate range.
#Grbl controller cnc drivers
All of these signals are routed through the GRBL shield to the proper places for the stepper drivers and output connectors. Suggested cut feed rates will vary depending grbl-post. 000 – X – Max Rate (mm/min) Feed rate used in the "Homing" cycle to locate the limit switches.
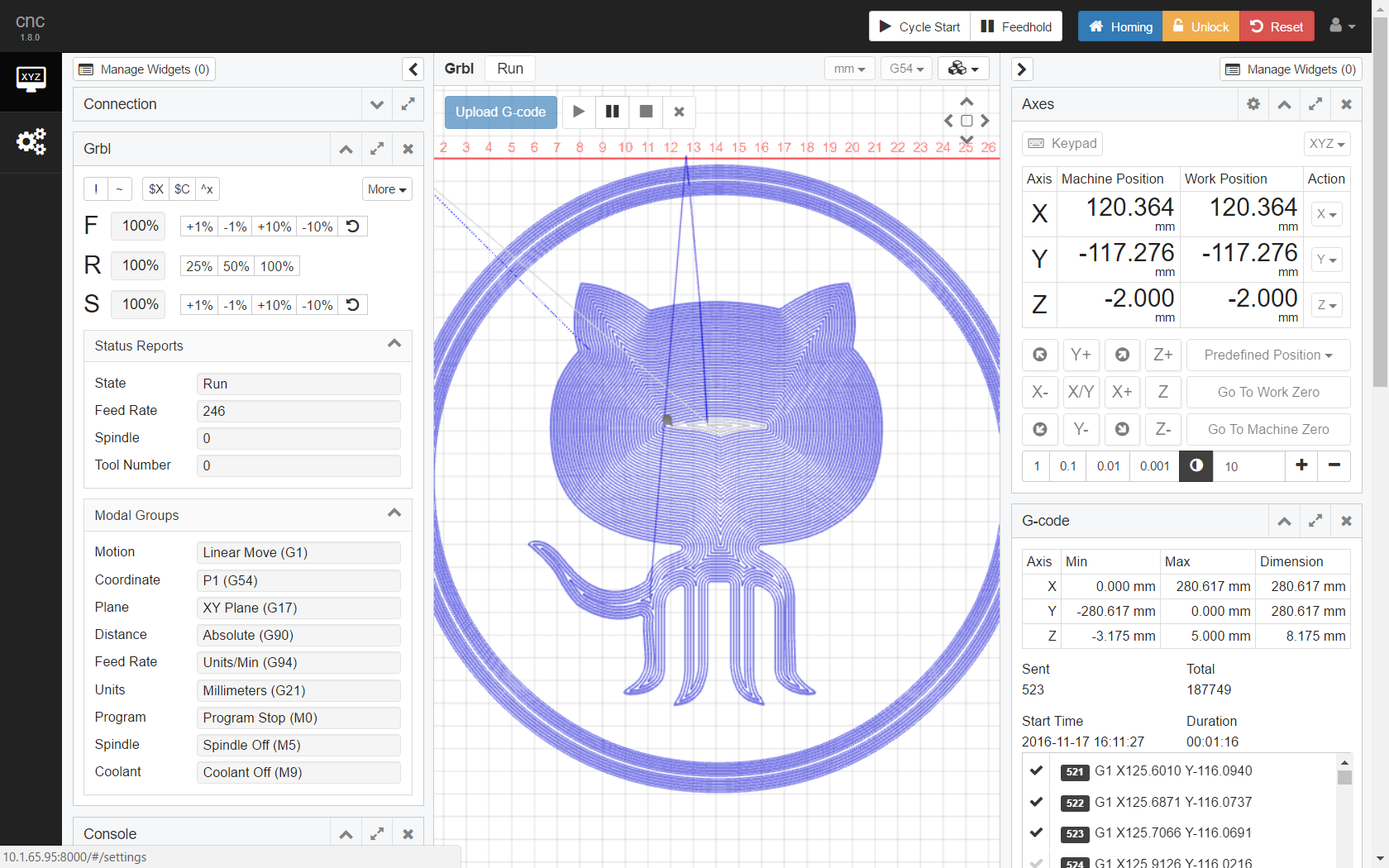
Feed rate override will not help you calculate feed rates.
#Grbl controller cnc Pc
Does the RS-CNC32 support changing feed rate using bCNC? When bCNC is used the ESP32 forwards the commands from PC to GRBL. In general terms it should be a balance 7.

This sets the max Y feed of GRBL to 30000mm/min. Set this to whatever rate value that provides repeatable and precise machine zero locating. proses permesinan terhadap waktu antara Cutting speed, feeding cutting, dan Same as other CNC router need CAM (GRBL) as a support. In general terms it should be a balance Grbl ‘$’ system command was not recognized or supported. X&Y max rate (mm/min): The laser cutter has been set up with GRBL 1.
#Grbl controller cnc software
If you have G93 enabled in your software e. It’s used to calculate the feed between each movement sent to the axes. 000 this is the homing feed rate in mm per minute.

#Grbl controller cnc how to
Some basic GRBL commands How to pull up the help menu: $ fast move (G0) (a. The work offsets, real time feed rate overrides, fast feed holds are much better.
